OOFELIE::Multiphysics for advanced optical systems
Integrated STOP analysis workflow
The keyword “STOP” refers to an investigation of structural, thermal, and optical performance. This type of analysis entails assessing and optimizing the performance of a system that combines optical, thermal, and mechanical components. It is especially important in the design and analysis of systems where optical parts are subjected to variable temperatures and mechanical stresses, such as lenses, mirrors, telescopes, lasers, and so on.
STOP stands for Structural Thermal Optical Performance:
Structural (S): This aspect involves analyzing the mechanical or structural integrity of the system. It entails assessing how the system’s various parts react to stresses such as vibrations and mechanical loads. This is necessary to ensure that the system can endure any environmental conditions that may arise.
Thermal (T): Thermal analysis is concerned with understanding and managing heat distribution within a system. Temperature changes in opto-thermomechanical systems can have an impact on the performance of optical components. Thermal analysis assists designers in ensuring that the system remains within permissible temperature ranges in order to preserve optical performance and avoid damage.
Optical (O): Evaluating the optical elements in the system in response to mechanical loads and temperature variations is part of the optical performance aspect. In order to make that the system satisfies its performance criteria under various circumstances, this entails examining indicators such as aberrations, image distortions, and other optical characteristics.
Performance (P): This often refers to the system’s total performance, taking into account both the optical and mechanical aspects. The goal is to optimize the design and settings so that the intended performance may be achieved in real-world operating situations.
Presentation of the link with OpticStudio
The OOFELIE::Multiphysics Solver is tightly combined with either RayJack ONE or OpticStudio through automated in-memory data exchange to help engineers accurately predict the behavior of optomechanical systems and MOEMS.
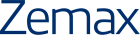
In a variety of optical applications, optical designs have to be combined with thermo-mechanical matters. For this reason, the OOFELIE::Multiphysics Solver automatically links either to RayJack ONE or OpticStudio optical design software.
While combining data from finite element analyses with ray-tracing tools typically requests time-consuming human operations, the automated in-memory data exchanges between OOFELIE::Multiphysics and an optical design software will guarantee you a fast, easy-to-use, and reliable design flow.
Beyond the so-called “STOP” analyses, this integrated solution also offers advanced modeling capabilities for the design of complex electro-optic devices such as MOEMS, including their steering mechanisms and active/adaptive optics.
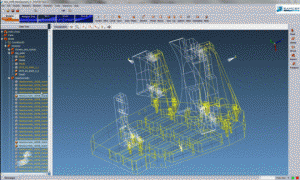
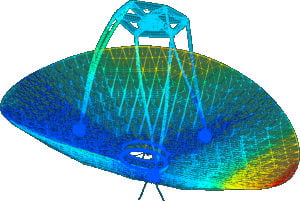
Features
To interact with the optical design software, the OOFELIE::Multiphysics Solver was provided with the following capabilities:
OOFELIE::Multiphysics link to Simcenter 3D
Key features
Highlights | Application Examples |
| Optical and multiphysics co-simulation analysis in:
|
Available features for this vertical application
The following physical fields are available in OOFELIE::Multipysics.
- Static and transient
- Linear and non-linear
- Modal
- Real and complex
- Wet-mode shapes
- Harmonic
- Random vibrations
- Strength assessment
- Topology optimization
- Density based (SIMP)
- Iso- and orthotropic materials:
- Viscous, viscoelastic and structural damping
- Perfectly matched layers (PML)
- 3D modelling
- (Oriented) Volume, membrane, shell, rod, beam, lumped mass elements
- Large displacements & pre-stress
- Identical nodes, contact, perfect/non-perfect mechanical gluing, rigid body assemblies, mean
- Special effects:
- Coriolis
- Centrifugal
- 2-ways coupling with:
- Thermal field
- Electrical field
- 1-way coupling with optics
- Static (steady-state) and transient
- Linear and non-linear
- Topology optimization
- Density based (SIMP)
- 3D modelling
- Identical nodes, perfect/non-perfect thermal gluing, thermal contact admittance
- 3D mutual radiation (ray tracing)
- Orbital model
- 2-ways coupling with
- Mechanical field
- Electrical field
- Static and transient;
- Linear and non-linear
- FEM / BEM coupling
- Dielectric materials
- Identical nodes
- Perfect/non-perfect electrical gluing
- RLC, electric dipole elements
- 2-ways coupling with
- Mechanical field
- Thermal field
- Static and Transient
- Linear
- Non-linear
- Any gas or liquid material (Newtonian behaviour)
- 3D, 2D planar and axisymmetric modelling
- Symmetry planes
- Incompressible & Boussinesq Law
- Boundary conditions
- Velocity and temperature at inlet
- Pressure at outlet
- Boundary conditions
- Non-slip flow
- Surface heat flux or temperature at walls
- 2-ways coupling with mechanical and thermal fields
- Physics
- Mechanical
- Thermal
- Static analysis
- Gradient based method with MMA optimizer
- Density-based approach
- Adjoint variable method for sensitivities computation
- Advanced SIMP laws
- Multimaterial with or without void
- Manufacturing constraint:
- Minimum member size
- Overhang
- Filters on:
- Sensitivities
- Densities
- Various objective and constraint functions
- Volume (Total or On specific material)
- Total mass
- Mechanical compliance
- Thermal compliance
- Displacement on points
- Rotation on points
- Temperature on points
- Eigen frequencies
- Uncertainty quantification in the model related to
- Loads definition
- Material properties specifications
The following couplings are accessible in OOFELIE::Multipysics.
- Static and Transient
- Linear and non-linear
- Complex Modal and Harmonic
- 3D modelling
- Thermo-elastic iso- and orthotropic materials
- Thermo-elastic damping effect
- Thermal dependency of material properties
- 2-ways coupling with electric field
- 1-way coupling with optics
- Coupling with Zemax’ OpticStudio
Automated data exchange via in-memory dialog - Description of surface deformations:
Zernike Standard or Fringe polynomials, grid of points, all aperture types - Rigid body motion recognition and ability to export separately to Zemax’ OpticStudio
- Thermo-optic effect:
- Accounting for refractive index change as a function of Temperature.
- Computation and visualization of refractive index gradients inside lenses.
- Automated exportation to Zemax’ OpticStudio
- FEM/BEM coupling
- Mesh morphing
- Fast Multipole Methods for BEM
- Pre-stress
- Pull-in voltage computation
- Static and transient
- Linear and non-linear
- Modal and harmonic
- Piezoelectric materials:
- Hexagonal C6
- Trigonal D3
- Triclinic C1
- Perfectly matched layers (PML)
- (Oriented) Volume, membrane, shell
- 2-ways coupling with thermal
- 1-way coupling with optics